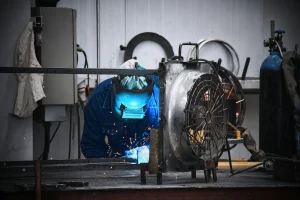
Critical Factors Affecting Vessel Post-Weld Quality
Pressure vessel post-weld represent critical components in numerous industries from oil and gas to chemical processing, power generation, and beyond. The integrity of these vessels directly impacts operational safety, regulatory compliance, and long-term reliability. Among the crucial fabrication steps that ensure pressure vessel quality, Vessel Post-Weld heat treatment (PWHT) stands as one of the most important yet often misunderstood processes. This carefully controlled thermal procedure transforms the metallurgical structure of welded joints, addressing challenges created during the welding process itself.
Understanding PWHT Fundamentals for Pressure Vessel post-weld
Vessel Post-weld heat treatment refers to controlled heating of a welded component to a specific temperature, holding at that temperature for a designated time, followed by controlled cooling. For pressure vessels, this process serves several crucial purposes that directly impact vessel integrity and service life.
Pressure vessel post-weld fabricated from carbon steel and low-alloy steels typically require PWHT when material thickness exceeds code-specified thresholds often around 1-1.5 inches depending on the specific material and code requirements. Certain high-stress applications or vessel post-weld intended for severe service environments may require PWHT regardless of thickness.
Critical Benefits of Vessel Post-Weld Heat Treatment
Stress Relief and Reduction of Residual Stresses
Perhaps the most recognized benefit of PWHT is stress relief. The welding process creates significant thermal gradients that result in locked-in residual stresses often approaching the yield strength of the material. These stresses combine with operational stresses, potentially exceeding design limits and contributing to premature failure.
PWHT reduces these residual stresses by allowing atoms to rearrange at elevated temperatures where yield strength is reduced. This stress reduction is particularly important in thicker vessel post-weld where high constraint can prevent natural stress relaxation during cooling.
Improvement of Mechanical Properties and Toughness
Proper PWHT transforms hard, brittle microstructures in the heat-affected zone into tougher, more ductile structures. This transformation significantly improves impact properties and fracture toughness critical factors in preventing brittle failure in pressure vessel post-weld.
Mitigation of Hydrogen-Induced Cracking
Welding processes often introduce hydrogen into the vessel post-weld metal and heat-affected zone. When combined with hardened microstructures and high residual stresses, this hydrogen can cause delayed cracking sometimes occurring days after welding completion.
Enhanced Corrosion Resistance in Service Environments
Many pressure vessel post-weld operate in corrosive environments where stress corrosion cracking poses a significant risk. By reducing residual stresses, PWHT directly mitigates this risk factor.
Additionally, PWHT can stabilize the microstructure in ways that enhance general corrosion resistance. This is particularly important in vessels handling corrosive media where even minor corrosion acceleration could compromise integrity and service life.
PWHT Methods and Implementation Practices
Local vs. Furnace Heat Treatment Options
Pressure vessel post-weld PWHT can be performed either in a furnace (complete vessel heat treatment) or through local methods. Furnace treatment provides the most uniform heating but may be impractical for large vessels or field applications.
Local PWHT employs electric resistance heating elements and thermal insulation to treat specific weld areas. While more complex to control, local methods enable treatment of vessels too large for furnaces or vessels already in field installations. Both approaches can provide code-compliant results when properly implemented and monitored.
Temperature Control and Monitoring Requirements
Precise temperature control represents one of the most critical aspects of successful PWHT. Temperatures must be maintained within relatively narrow ranges typically ±25°F of the target temperature throughout the heated zone.
This control requires strategic thermocouple placement, with recording instruments continuously documenting temperature profiles. Modern systems typically employ multiple thermocouples and computerized monitoring to ensure compliance with procedure requirements and create permanent records of the thermal cycle.
Heating and Cooling Rate Management
Controlled heating and cooling rates prevent thermal shock and excessive thermal gradients that could create new stresses or damage. Typical heating rates range from 100°F to 400°F per hour, depending on material thickness and type.
Cooling rates after the holding period must be similarly controlled, often requiring slower rates through critical temperature ranges where metallurgical transformations occur. These carefully managed rates ensure the PWHT achieves stress relief without introducing new problems.
Soak Time Determination for Different Materials
The duration of the holding period at temperature commonly called “soak time”depends primarily on material thickness and type. Codes typically specify minimum soak times of one hour per inch of thickness, with minimum times regardless of thickness.
ASME Code Requirements for Pressure Vessel post-weld PWHT
Material-Specific PWHT Requirements
The ASME Boiler and Pressure Vessel post-weld Code provides detailed requirements for PWHT based on material classification. Section VIII, Division 1 includes specific tables outlining when PWHT is mandatory based on material type and thickness.
Thickness Considerations and Exemption Criteria
Material thickness significantly impacts PWHT requirements, with thicker materials generally requiring treatment at lower thickness thresholds. The code also provides specific exemption criteria for certain joint configurations, preheating conditions, or specialized applications.
Understanding these exemptions requires careful code review and often involves engineering analysis to ensure that alternative approaches provide equivalent safety. These determinations must be documented as part of the vessel’s quality records.
Documentation and Quality Control Procedures
PWHT documentation requirements include detailed procedures, qualification records, time-temperature charts, thermocouple placement diagrams, and verification of equipment calibration. These records form an essential part of the vessel’s permanent documentation package.
Quality control procedures must verify that all aspects of the PWHT meet code requirements and that the results achieve the intended metallurgical objectives. This often includes hardness testing, review of temperature charts, and sometimes mechanical testing of representative samples.
Common Compliance Challenges and Solutions
Uniform heating of complex geometries presents a common challenge, particularly around thickness transitions or nozzles. Solutions include customized heating element layouts, additional insulation, and strategic thermocouple placement to monitor potential cold or hot spots.
Need a reliable partner?
Red River specializes in the design and manufacturing of pressure vessels. We also fabricate related items such as prefabricated spools and skid packages.
Reach out to us today and experience the Red River difference. Where American-made products and American Values come together, we care more.
Frequently Asked Questions (FAQ)
1. When is vessel post-weld heat treatment mandatory for pressure vessels?
PWHT becomes mandatory based on material type, thickness, and service conditions as specified in applicable codes like ASME Section VIII. For common carbon steels (P-No. 1 materials), PWHT is typically required when thickness exceeds 1.5 inches. For alloy steels like chrome-moly (P-No. 4 materials), PWHT may be required regardless of thickness. Additionally, vessel post-weld intended for severe service environments including those susceptible to stress corrosion cracking or operating at very low temperatures often require PWHT regardless of thickness.
2. What happens if PWHT is not performed when required by code?
Omitting required PWHT creates several serious consequences. First, the vessel cannot be legally stamped or certified under the applicable code, making it unusable for its intended purpose. From a technical perspective, the vessel remains susceptible to failures from residual stress, hydrogen cracking, and poor fracture toughness. These conditions significantly increase the risk of catastrophic failure during hydrostatic testing or early service. Retrofitting PWHT is often extremely difficult after completion, potentially requiring complete vessel replacement.
3. How do different materials affect PWHT parameters for pressure vessel post-weld?
Different materials require specific PWHT parameters. Carbon steels typically need heating to 1100-1200°F for relatively straightforward stress relief. Low-alloy steels like 2.25Cr-1Mo require more precise temperature control—often 1250-1350°F—with longer soak times to ensure proper transformation of alloying elements. Stainless steels often require specialized treatments; for example, austenitic stainless steels rarely need conventional PWHT but may require solution annealing at much higher temperatures (1900°F+) for certain applications.
4. What is the difference between stress relieving and full annealing in PWHT?
Stress relieving typically involves heating to lower temperatures (1100-1250°F for carbon steels) with the primary goal of reducing residual stresses without significantly altering the base microstructure. Full annealing involves heating to higher temperatures (typically above 1600°F for carbon steels), holding, and then very slow cooling. Annealing completely recrystallizes the microstructure, removing work hardening and creating a more uniform, softer material. Pressure vessel post-weld PWHT usually employs stress relieving rather than full annealing, as the latter would reduce strength below design requirements.
5. How are temperature and heating rates monitored during pressure vessel post-weld PWHT?
Temperature monitoring employs thermocouples attached directly to the vessel surface at strategic locations. Modern practice typically uses a minimum of one thermocouple per heating zone, with additional thermocouples at potential cold spots or critical areas. These thermocouples connect to calibrated recording instruments that continuously document the time-temperature profile. Digital recording systems automatically compare actual temperatures with procedure requirements and alert operators to deviations. The complete temperature record becomes part of the vessel post-weld permanent documentation.
Key Takeaways
- PWHT is essential for ensuring pressure vessel post-weld integrity and longevity by addressing metallurgical changes created during welding
- Proper temperature control and documentation are critical for code compliance and verifiable quality assurance
- Material selection directly impacts PWHT requirements and procedures, with each material type requiring specific approaches
- Skipping required PWHT can lead to premature failure through mechanisms like stress corrosion cracking and hydrogen embrittlement
- Investment in proper PWHT procedures provides long-term reliability benefits that far outweigh the additional fabrication costs