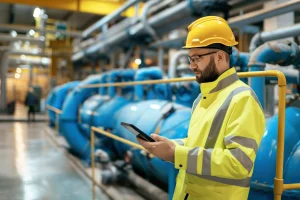
Key Considerations for Pressure Vessel Quality
Pressure vessel quality represent critical components in numerous industries, from oil and gas to chemical processing and power generation. Pressure Vessel Quality is paramount, as the integrity of these vessels directly impacts operational safety, regulatory compliance, and long-term reliability. At the heart of successful pressure vessel manufacturing lies a robust Quality Assurance Plan (QAP) ,a systematic approach that ensures every vessel meets stringent industry standards while minimizing risks and costs. Therefore, Pressure Vessel Quality must be the highest concern.
What is a Quality Assurance Plan in Pressure Vessel Manufacturing?
A Qaulity Assurance Plan for pressure vessel quality fabrication is a comprehensive document that outlines the procedures, inspections, and documentation required to verify that a pressure vessel meets all applicable codes, standards, and customer specifications. Unlike general manufacturing QAPs, those designed for pressure vessel quality must address unique risk factors associated with containing pressurized media.
Regulatory bodies like the American Society of Mechanical Engineers (ASME) through their Boiler and Pressure Vessel Code (BPVC), as well as organizations like the American Petroleum Institute (API), establish the fundamental requirements that must be addressed in pressure vessel QAPs. These codes don’t merely suggest best practices they establish legally mandated safety standards.
It’s important to distinguish between Quality Assurance (QA) and Quality Control (QC) in the pressure vessel context. While QA focuses on the systematic processes and procedures that prevent defects, QC involves the actual inspections and tests that verify compliance. An effective pressure vessel QAP integrates both approaches for maximum effectiveness.
Key Components of an Effective Pressure Vessel QAP
Material Verification and Traceability Requirements
Material integrity forms the foundation of pressure vessel quality and safety. An effective QAP establishes protocols for verifying that all materials meet specified requirements before fabrication begins. This includes confirming that Material Test Reports (MTRs) match engineering specifications and that traceability systems are in place to track materials from receipt through final assembly. For critical applications, positive material identification (PMI) testing may be required to verify chemical composition.
Welding Procedure Qualification and Documentation
Welding represents one of the most critical aspects of pressure vessel fabrication. QAPs must address Welding Procedure Specifications (WPS), Procedure Qualification Records (PQR), and welder qualification testing. Each welding procedure must be validated to ensure it produces joints with mechanical properties suitable for the vessel’s intended service conditions. Comprehensive documentation of these qualifications provides the foundation for consistently high-quality welded joints.
Inspection Hold Points and Documentation
Effective QAPs establish strategic inspection hold points throughout the fabrication process. These mandatory pauses allow for verification that critical steps meet quality requirements before work proceeds. Common hold points include material receipt inspection, fit-up verification before welding, examination of completed welds, and pre-hydrostatic test inspections. Each hold point requires specific documentation to maintain a complete quality record.
Nondestructive Examination (NDE) Protocols
NDE techniques like radiographic testing (RT), ultrasonic testing (UT), magnetic particle testing (MT), and penetrant testing (PT) provide crucial verification of joint integrity without damaging the vessel. A comprehensive QAP specifies which NDE methods apply to different joint types, acceptance criteria for each examination, and qualification requirements for NDE personnel. The QAP must also address documentation standards for examination results.
Implementing Your QAP Throughout the Fabrication Process
Pre-fabrication Planning and Documentation
Quality begins before manufacturing starts. The pre-fabrication phase includes detailed review of design documentation, verification that all materials and consumables meet specifications, and confirmation that all required procedures and qualifications are in place. This phase also includes developing inspection and test plans (ITPs) that will guide quality verification activities throughout fabrication.
In-process Quality Control Measures
During fabrication, the QAP guides ongoing verification activities. These include dimensional checks, visual inspections of weld preparation and completed welds, and verification that all work follows approved procedures. In-process controls also monitor environmental conditions that could affect quality, such as ambient temperature during welding or heat treatment.
Final Inspection and Testing Requirements
The final verification phase typically includes hydrostatic or pneumatic testing to verify pressure integrity, dimensional verification, and comprehensive visual inspection. For coded vessels, this phase often includes witness points for authorized inspectors who verify compliance with regulatory requirements. The QAP specifies acceptance criteria for each test and inspection.
Documentation and Records Management
A pressure vessel quality without proper documentation has limited utility and may not be legally operational. The QAP establishes requirements for assembling, reviewing, and maintaining the documentation package, which typically includes material certifications, examination records, test reports, and the all-important Manufacturer’s Data Report.
Benefits of Comprehensive Pressure Vessel Quality Assurance Plans
Implementing rigorous QAPs delivers multiple benefits beyond mere regulatory compliance. A well-executed quality program significantly reduces the likelihood of costly rework by catching potential issues early in the fabrication process. This proactive approach typically reduces overall manufacturing costs despite the investment in quality activities.
From a safety perspective, comprehensive pressure vessel quality assurance directly correlates with improved vessel integrity, reducing the risk of catastrophic failures that could threaten personnel safety and environmental protection. Furthermore, vessels manufactured under robust quality systems typically deliver longer service life with fewer maintenance issues, improving the total cost of ownership.
Common Challenges in QAP Implementation
Despite their clear benefits, implementing effective QAPs presents several challenges. Many organizations struggle with allocating sufficient resources both personnel and budget to quality activities. Training and maintaining qualified quality personnel represents another significant challenge, particularly for specialized inspections.
Managing the substantial documentation generated through pressure vessel quality processes requires robust systems, whether paper-based or digital. Modern QA approaches increasingly leverage technology, including digital documentation systems, automated inspection technologies, and integrated pressure vessel quality management software to improve efficiency and effectiveness.
Need a reliable partner?
Red River specializes in the design and manufacturing of pressure vessels. We also fabricate related items such as prefabricated spools and skid packages.
Reach out to us today and experience the Red River difference. Where American-made products and American Values come together, we care more.
Frequently Asked Questions (FAQ)
1. What codes and standards govern pressure vessel Quality Assurance Plans?
Pressure vessel quality QAPs are primarily governed by the ASME Boiler and Pressure Vessel Code (BPVC), particularly Section VIII for pressure vessels. Depending on the application, additional standards may apply, including API 510 for in-service inspection, NBIC standards for repairs, and various international codes like PED in Europe or AS1210 in Australia.
2. How often should a pressure vessel QAP be reviewed and updated?
QAPs should be reviewed at least annually and updated whenever significant changes occur in applicable codes, manufacturing processes, or organizational structure. Additionally, reviews should follow any quality issues that indicate potential gaps in the existing plan. Many organizations align QAP reviews with their management system audit schedule.
3. What qualifications should QA/QC personnel have for pressure vessel inspection?
Key certifications include Certified Welding Inspector (CWI) from the American Welding Society, API Inspector certifications, and ASNT NDT Level II or III for those performing nondestructive examinations. Familiarity with ASME code requirements is essential, and many companies require inspectors to have formal training on specific codes and standards.
4. How do material test reports (MTRs) factor into pressure vessel Quality QAPs?
MTRs provide critical verification that materials meet chemical composition and mechanical property requirements specified in the design. QAPs typically require verification that MTRs match purchase specifications, confirmation that materials are properly marked for traceability, and systems to ensure that only materials with appropriate documentation enter the fabrication process.
5. What documentation must be retained after pressure vessel quality fabrication?
Required documentation typically includes the Manufacturer’s Data Report (ASME U-1, U-2, or U-3 forms for code vessels), material test reports for pressure boundary components, examination records for all required NDE, heat treatment records, pressure test results, and records of any repairs. This documentation package should be retained for the life of the pressure vessel quality.
6. How do digital technologies improve pressure vessel quality assurance?
Digital technologies streamline quality processes through electronic documentation systems that improve access and reduce errors, automated inspection technologies that enhance detection capabilities, and integrated quality management software that facilitates workflow and compliance verification. Emerging technologies like digital radiography and 3D scanning are increasingly improving inspection capabilities.
7. What are the consequences of inadequate quality assurance for pressure vessel quality?
Inadequate pressure vessel quality assurance can lead to serious consequences including regulatory non-compliance and potential fines, vessel failure causing injury or environmental damage, extensive rework costs, project delays, and damage to company reputation. Many jurisdictions impose legal liability for failures resulting from quality deficiencies.
Key Takeaways
- QAPs are essential for code-compliant pressure vessel quality abrication, providing the framework for consistent quality outcomes
- Proper implementation requires a systematic approach and comprehensive documentation from material receipt through final testing
- Investing in pressure vessel quality assurance reduces long-term costs by minimizing rework and extending vessel service life
- Working with experienced fabricators ensures proper QAP execution through established procedures and qualified personnel
- Comprehensive quality documentation establishes a valuable record of compliance that supports pressure vessel quality registration and future inspections