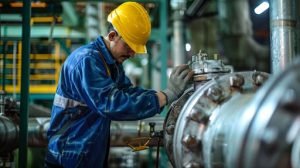
Essential Requirements for ASME Pressure Vessel Inspection
Pressure vessel Inspection are critical components in many industrial operations across the United States. These containers, designed to hold gases or liquids at pressures substantially different from ambient conditions, require rigorous inspection to ensure workplace safety and operational reliability. Understanding proper inspection procedures isn’t just about regulatory compliance, it’s essential for preventing catastrophic failures and protecting personnel.
Understanding Pressure Vessel Inspection Requirements
Pressure vessel inspections aren’t optional in U.S. facilities—they’re mandated by federal and state regulations. These inspections help identify potential issues before they become dangerous and ensure vessels maintain their integrity throughout their service life.
ASME Boiler and Pressure Vessel Code Basics
The American Society of Mechanical Engineers (ASME) Boiler and Pressure Vessel Code establishes the foundation for pressure vessel inspection requirements. Section VIII of the code specifically addresses pressure vessels, outlining construction standards, materials, fabrication requirements, and inspection protocols. Most U.S. jurisdictions have adopted these standards as legal requirements.
Types of Pressure Vessel Inspection
Regulatory Agencies Overseeing Inspections
Several authorities enforce pressure vessel inspection compliance, including:
- State and local jurisdictions through inspection departments
- Insurance companies with authorized inspectors
- The Occupational Safety and Health Administration (OSHA)
- The National Board of Boiler and Pressure Vessel Inspectors
Most pressure vessel inspection require inspection at installation, periodically during service, and after significant repairs or alterations. Standard intervals typically range from 1-3 years, depending on vessel type, application, and local regulations.
Comprehensive pressure vessel inspection programs incorporate multiple examination approaches to ensure thorough evaluation of all potential failure points.
External Visual Inspections
External inspections can often be performed while vessels remain in service. Inspectors examine:
- External surfaces for corrosion, mechanical damage, or distortion
- Structural supports and attachments
- Pressure relief devices and their settings
- Instrumentation and controls
- Evidence of leaks or deterioration
These inspections typically occur annually but may be more frequent in corrosive environments.
Internal Visual Inspections
Internal inspections require vessels to be taken offline, opened, and thoroughly examined from the inside. Inspectors look for:
- Internal corrosion or erosion
- Crack development, especially at welds
- Damage to internal components
- Lining deterioration (if applicable)
- Evidence of overheating
Most pressure vessels require internal inspection every 3-5 years, though this varies based on service conditions and vessel history.
Non-Destructive Testing Methods
Beyond visual inspection, several non-destructive testing (NDT) methods provide deeper insights into vessel condition:
- Ultrasonic thickness testing to measure wall thickness
- Magnetic particle testing to detect surface and near-surface flaws
- Radiographic testing to examine welds and internal components
- Liquid penetrant testing to identify surface cracks
- Acoustic emission testing to detect active defects under stress
Each inspection must be properly documented, with records detailing findings, measurements, and recommendations.
Step-by-Step Inspection Procedure
A standardized approach to pressure vessel inspection ensures consistency and thoroughness in the examination process.
Pre-Inspection Preparation
Before inspection begins:
- Review previous inspection reports and vessel documentation
- Verify all energy sources are isolated (lockout/tagout)
- Properly clean the vessel for thorough examination
- Ensure adequate ventilation and test for hazardous atmospheres
- Prepare appropriate access equipment (scaffolding, ladders)
Safety Protocols During Inspection
Safety remains paramount during inspections:
- Obtain confined space entry permits if required
- Use appropriate personal protective equipment
- Maintain continuous atmospheric monitoring
- Establish communication protocols with safety attendants
- Have rescue procedures and equipment ready
Documentation and Reporting Requirements
Comprehensive documentation includes:
- Vessel identification information (serial number, national board number)
- Inspection date and type of inspection
- Inspector qualifications and certification
- Detailed findings with measurements and photographs
- Recommendations for repairs or future monitoring
- Certification of inspection completion
Compliance and Certification
Maintaining vessel compliance requires ongoing attention to inspection findings and certification requirements.
Maintaining Inspection Records
Proper record-keeping includes:
- Maintaining historical inspection data for each vessel
- Documenting all repairs or alterations
- Tracking inspection due dates
- Keeping certificates of operation current
- Retaining manufacturer’s data reports
Addressing Inspection Findings
When inspections reveal issues:
- Categorize findings by severity and required response time
- Develop repair plans that comply with code requirements
- Use only qualified personnel for repairs
- Conduct post-repair inspections before returning to service
- Update vessel documentation to reflect changes
Many facilities overlook the requirement that alterations to pressure vessels must receive the same level of inspection and certification as new construction—a common compliance gap during audits.
Need a reliable partner?
Red River specializes in the design and manufacturing of pressure vessels. We also fabricate related items such as prefabricated spools and skid packages.
Reach out to us today and experience the Red River difference. Where American-made products and American Values come together, we care more.
Frequently Asked Questions
1. How often must pressure vessel inspection be inspected in U.S. plants?
External inspections are typically required annually, while internal inspections usually occur every 3-5 years. However, inspection frequency can vary based on vessel type, contents, operating conditions, and local regulations. High-risk applications or vessels with known issues may require more frequent inspection.
2. Who is qualified to perform pressure vessel inspections?
Official inspections must be conducted by authorized inspectors who hold current commissions from the National Board of Boiler and Pressure Vessel Inspectors. These inspectors typically work for insurance companies or state/local jurisdictional authorities. In-house personnel may perform informal monitoring, but certified inspectors must conduct regulatory inspections.
3. What are the most common pressure vessel inspection failures?
Common inspection failures include excessive corrosion or erosion, cracked welds, damaged supports, inoperable pressure relief devices, inadequate documentation, and unauthorized repairs or modifications. Corrosion accounts for approximately 70% of all pressure vessel failures identified during inspections.
4. Are inspection requirements different for different types of pressure vessels?
Yes, pressure vessel inspection requirements vary based on vessel classification, size, contents, and operating pressure. For example, high-pressure vessels, those containing hazardous materials, or vessels with a history of issues typically require more comprehensive and frequent inspections. Some small vessels used in non-hazardous applications may qualify for reduced inspection requirements.
5. What documentation must be maintained for pressure vessel inspections?
Essential documentation includes the manufacturer’s data report (U-1 or U-2 form), installation certification, inspection reports, repair/alteration records (R-1 forms), operating certificates, vessel registration, relief valve certifications, and any non-destructive examination reports.
6. How do I prepare a pressure vessel inspection?
Proper preparation includes shutting down and isolating the vessel, relieving pressure, draining contents, properly cleaning internal surfaces, removing insulation as needed, providing adequate lighting and access, and ensuring all safety measures for confined space entry are in place.
7. What happens if my pressure vessel inspection fail?
If a vessel fails inspection, the inspector will document deficiencies and may issue a repair recommendation or, in severe cases, an order to remove the vessel from service. Repairs must be performed by qualified personnel, typically holding “R” stamp certification, and must be reinspected before the vessel returns to service.
Key Takeaways
- Pressure vessel inspections are legally required and critical for safety
- Inspection frequency varies based on vessel type, contents, and service conditions
- Proper documentation is essential for regulatory compliance
- Only qualified pressure vessel inspections should perform formal vessel inspections
- Addressing inspection findings promptly prevents escalation of issues
- Maintaining thorough records protects facilities during regulatory reviews