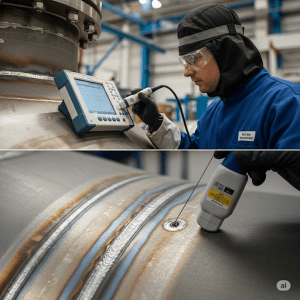
Vessel Weld Quality Acceptance Criteria Per ASME Standards
Pressure vessels serve as critical components in numerous industries, from oil and gas processing to chemical manufacturing, power generation, and beyond. These vessels contain gases and liquids under significant pressure, making their structural integrity paramount to operational safety. At the heart of pressure vessel reliability lies Vessel Weld Quality, the careful execution and verification of joints that must withstand extreme conditions for decades of service.
Why Vessel Weld Quality Control Is Critical for Pressure Vessel Safety
Vessel Weld Quality represents the most critical factor in pressure equipment reliability, as welds inherently constitute potential weak points in any pressure vessel’s structure. The assessment and verification of Vessel Weld Quality demands exceptional attention because, unlike the base material which undergoes rigorous testing and certification before fabrication begins, welds are created during the manufacturing process itself. Superior Vessel Weld Quality must be meticulously controlled through every stage of fabrication to ensure these critical joints match or exceed the strength and durability of the surrounding material.
Essential Elements of a Pressure Vessel Weld Quality Program
Welding Procedure Specification (WPS) Development and Qualification
Every successful weld begins with a properly developed and qualified Welding Procedure Specification (WPS). This document details all essential variables from base material and filler metal selection to preheat requirements, electrical parameters, and post-weld heat treatment specifications. For pressure vessel weld quality, these WPS documents must be qualified through rigorous testing that verifies the resulting welds meet or exceed all mechanical and metallurgical requirements.
Welder Qualification and Certification Requirements
Even the best procedure remains ineffective without skilled welders qualified to execute it. Welder qualification testing verifies that specific individuals possess the skills to produce code-compliant welds using given procedures. These qualifications must be periodically renewed and are typically position and process-specific.
For pressure vessel weld quality fabrication, welder qualifications must comply with ASME Section IX requirements, which define essential variables and testing protocols. Records of these qualifications must be meticulously maintained and made available for verification by authorized inspectors and customer representatives.
Material Preparation and Fit-Up Inspection
Quality welds begin with proper material preparation and fit-up. Prior to welding, edges must be properly beveled, cleaned, and aligned with appropriate root gaps and alignment tolerances. These parameters are specified in the WPS and must be verified before welding begins.
Inspections at this stage prevent issues that could otherwise be hidden by the completed weld. Proper fit-up ensures adequate penetration can be achieved, while material cleanliness prevents contamination that could lead to defects like porosity or inclusions.
In-Process Weld Monitoring Techniques
Throughout the welding process, ongoing monitoring ensures compliance with the qualified procedure. This includes verification of preheat and interpass temperatures, monitoring of electrical parameters like amperage and voltage, and visual inspection of each pass before subsequent layers are applied.
Non-Destructive Examination Methods for Pressure Vessel Weld Quality
Radiographic Testing (RT) Applications and Limitations
Radiographic testing using X-rays or gamma rays to create images of weld internals remains the gold standard for volumetric inspection of many pressure vessel weld quality. This method excels at detecting volumetric defects like porosity, inclusions, and internal cracks.
However, RT has limitations, including sensitivity to defect orientation and challenges with thick materials or complex geometries. Safety requirements for radiation also impact production scheduling and accessibility. Despite these challenges, radiography provides permanent records of weld quality that can be reviewed by multiple parties.
Ultrasonic Testing (UT) for Weld Integrity Verification
Ultrasonic testing uses high-frequency sound waves to detect and characterize defects within welds. Modern techniques like phased array UT provide detailed imaging capabilities that can precisely locate and size defects. UT excels at detecting planar defects like lack of fusion or cracks that might be missed by radiography.
Liquid Penetrant Testing (PT) for Non-Magnetic Materials
For non-magnetic materials like stainless steel, aluminum, or titanium, liquid penetrant testing provides reliable surface defect detection. This method uses colored or fluorescent liquids that penetrate surface-breaking defects, making them clearly visible under proper lighting conditions.
PT offers simplicity and cost-effectiveness but is limited to surface defects only. It requires thorough cleaning both before testing and after completion to remove all chemical residues that could affect material performance.
Documentation and Traceability in Vessel Weld Quality Control
Essential Records for Regulatory Compliance
Comprehensive documentation provides the foundation for regulatory compliance and future reference. Essential records include WPS and PQR documentation, welder qualification records, material certifications for both base materials and filler metals, heat treatment records, and examination results.
These records must be maintained throughout the vessel’s lifecycle and made available for review during initial certification, in-service inspections, and any repair or alteration activities.
Weld Maps and Identification Systems
Weld maps provide visual references that identify each weld’s location, type, welder, and examination requirements. These maps link physical welds to their associated documentation, creating traceability essential for both quality control and future reference.
Identification systems typically include unique identifiers for each weld, often permanently marked near the weld location or documented in a manner that allows future inspectors to correlate examination findings with specific locations.
Final Documentation Package Requirements
Upon completion, pressure vessel weld quality require comprehensive documentation packages that typically include:
- Design calculations and drawings
- Material certifications
- Welding procedure and qualification records
- Examination reports for all required testing
- Heat treatment records
- Pressure test results
- Final dimensional reports
This package forms part of the vessel’s permanent record and provides essential information for future inspections or modifications.
The pursuit of exceptional Vessel Weld Quality remains a cornerstone of pressure equipment safety and reliability across all industries where these critical components operate. As this comprehensive examination has demonstrated, Vessel Weld Quality depends on multiple interconnected factors from material selection and joint design to welding procedures, execution, inspection, and documentation. Each element contributes to the ultimate integrity of pressure-containing joints that must perform flawlessly under demanding conditions.
Need a reliable partner?
Red River specializes in the design and manufacturing of pressure vessels. We also fabricate related items such as prefabricated spools and skid packages.
Reach out to us today and experience the Red River difference. Where American-made products and American Values come together, we care more.
Frequently Asked Questions (FAQ)
1. What are the most common weld defects in pressure vessel weld quality fabrication?
The most common weld defects include porosity (gas bubbles trapped within the weld, lack of fusion (failure of the vessel weld quality metal to fuse properly with the base metal), incomplete penetration (insufficient weld metal through the joint thickness), undercut (grooves melted into the base metal and left unfilled), and cracking (which may occur during welding or after cooling). Each defect type has specific causes, detection methods, and acceptance criteria defined by applicable codes.
2. How do ASME code requirements for vessel weld quality differ by vessel class?
ASME Section VIII Division 1 represents the most commonly used standard and provides relatively straightforward acceptance criteria for weld quality. Division 2 (Alternative Rules) imposes more rigorous requirements, including greater emphasis on fatigue analysis and typically more extensive examination. This often includes higher percentages of welds requiring volumetric examination and stricter acceptance criteria for defects. Division 3 covers high-pressure vessels with even more stringent requirements, recognizing the increased risk associated with higher pressures.
3. What qualifications should weld inspectors have for pressure vessel weld quality production?
Weld inspectors for pressure vessel weld quality typically need Certified Welding Inspector (CWI) credentials from the American Welding Society or equivalent qualifications. For performing non-destructive examinations, certification to ASNT SNT-TC-1A or similar standards is required, with Level II or III certification appropriate for final acceptance inspections. For ASME code vessels, the Authorized Inspector (employed by an authorized inspection agency) must have a commission from the National Board of Boiler and Pressure Vessel Inspectors.
4. How does material type affect vessel weld quality control requirements?
Different materials require specific quality control approaches. Carbon steels generally have straightforward requirements, while low-alloy steels often need preheat and post-weld heat treatment with careful temperature control. Stainless steels require protection from contamination and control of ferrite content in austenitic grades. Nickel alloys and non-ferrous materials like aluminum have unique challenges regarding heat input, filler selection, and cleanliness requirements. The inspection methods may also vary, with magnetic particle testing suitable only for ferromagnetic materials.
5. What documentation must be maintained for pressure vessel weld quality?
Essential documentation includes Welding Procedure Specifications (WPS), Procedure Qualification Records (PQR), Welder Performance Qualification Records (WPQR), weld maps identifying each weld and its corresponding welder, non-destructive examination reports, repair documentation if applicable, and final acceptance records. These records must be maintained for the service life of the vessel weld quality and must be available for review during inspections. Digital record systems increasingly supplement traditional paper documentation.
Key Takeaways
- Comprehensive vessel weld quality control is essential for pressure vessel safety, forming the foundation of structural integrity
- Proper procedure qualification and welder certification establish the fundamental requirements for quality welding
- Non-destructive examination confirms weld integrity before vessel commissioning, with each method offering specific advantages
- Complete documentation provides traceability throughout the vessel’s lifecycle, supporting regulatory compliance and future maintenance
- Investment in quality control prevents costly failures and ensures compliance with increasingly stringent safety standards