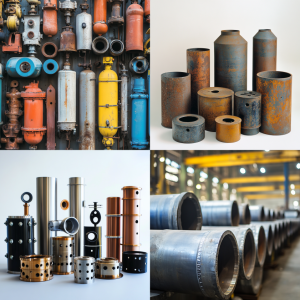
Selecting the Right Materials for Water Pressure Vessel Corrosion Protection
In the world of industrial and municipal operations, few components are as vital—and as vulnerable—as water pressure vessels. These vessels are foundational to systems ranging from water treatment plants and power stations to manufacturing facilities and municipal infrastructure. But while their function is critical, so too is their integrity. Corrosion remains one of the biggest threats to these vessels’ long-term performance and safety.
Choosing the right corrosion-resistant materials for pressure vessels is not just a matter of longevity—it’s a matter of compliance, safety, cost-efficiency, and operational reliability. Effective pressure vessel corrosion protection strategies are essential for ensuring your equipment performs reliably for years to come. Let’s dive into why this matters, the materials that get the job done, and how to make the right choices for your application.
Why Corrosion Resistance Matters in Water Pressure Vessels
The Role of Water Pressure Vessels in Industrial, Municipal, and Commercial Applications
Water pressure vessels play a key role in controlling and stabilizing pressure in fluid systems. In many industries, these vessels store water or process fluids under high pressure, ensuring smooth operation across pumps, filtration systems, and chemical applications.
Whether in municipal water systems, power generation, chemical manufacturing, or food processing, water pressure vessels are built to withstand immense stress. They must retain structural integrity across fluctuating temperatures, fluid types, and pressure loads—making the materials they’re made from crucial for pressure vessel corrosion protection.
The Constant Threat of Internal and External Corrosion
These vessels are constantly exposed to both internal corrosion (from the water or chemicals they hold) and external corrosion (due to environmental exposure, humidity, or industrial contaminants). Implementing proper pressure vessel corrosion protection measures becomes critical when dealing with corrosive agents such as:
- Oxygen and salts in the water
- Acids or chemicals used in processing
- High humidity or coastal environments
can gradually degrade metal surfaces, weakening the vessel and compromising safety.
Left unchecked, this corrosion can result in:
- Pitting (localized corrosion)
- Crevice corrosion (from stagnant water in small gaps)
- Galvanic corrosion (when dissimilar metals come in contact)
Without adequate pressure vessel corrosion protection, these issues can escalate quickly and compromise vessel integrity.
For a deeper understanding of how these separation processes occur and how materials respond under different conditions, refer to Britannica’s page on Separation Processes.
Risks of Corrosion: Structural Failure, Leaks, Safety Hazards, and Maintenance Costs
When corrosion goes unnoticed—or isn’t proactively addressed through pressure vessel corrosion protection measures—the consequences can be severe:
- Structural failure: Pressure vessels can rupture under stress, especially if corrosion thins the walls or weakens welds
- Leaks: Even small leaks can result in water loss, downtime, and contamination
- Increased maintenance: Frequent inspections, patchwork repairs, and premature replacements add up quickly
- Safety risks: A failed pressure vessel can pose threats to workers, facilities, and the environment
All of this makes pressure vessel corrosion protection not just desirable, but absolutely essential in pressure vessel design.
Common Corrosion-Resistant Materials Used in Water Pressure Vessels
The best way to achieve effective pressure vessel corrosion protection? Start with the right materials. Depending on your budget, application, and environmental factors, several options offer excellent pressure vessel corrosion protection for water pressure vessels.
Stainless Steel
Stainless steel is often considered the gold standard for pressure vessel corrosion protection.
- High chromium content (usually 10.5% or more) forms a passive film on the surface, protecting it from rust and chemical attack
- Highly durable and retains strength under pressure and heat
- Ideal for high-purity applications, such as food-grade water systems, pharmaceuticals, and potable water tanks
For example, Red River offers custom stainless steel fabrication tailored to industrial needs with superior pressure vessel corrosion protection.
Duplex Stainless Steel
Duplex stainless steel combines the strength of ferritic steel with advanced pressure vessel corrosion protection properties of austenitic steel.
- Contains higher levels of chromium, molybdenum, and nitrogen, making it extremely resistant to chloride stress corrosion cracking
- Stronger than traditional stainless steel, allowing for thinner walls and lower material costs
- Often used in high-pressure or saltwater environments, such as offshore platforms and chemical plants
This material balances performance and cost, making it an efficient pressure vessel corrosion protection solution for aggressive environments.
Fiberglass Reinforced Plastic (FRP)
FRP is a non-metallic composite material that provides excellent pressure vessel corrosion protection made from a polymer matrix reinforced with fiberglass.
- Lightweight and corrosion-resistant, especially in highly acidic or alkaline environments
- Non-conductive and won’t rust, making it ideal for chemical storage, wastewater treatment, and corrosive liquid containment
- Unlike metal vessels, FRP doesn’t suffer from galvanic corrosion, providing inherent pressure vessel corrosion protection
Coated Carbon Steel
Carbon steel is strong and affordable but prone to corrosion. That’s where pressure vessel corrosion protection coatings come in.
- Applying epoxy linings, rubber coatings, or zinc galvanization can significantly boost pressure vessel corrosion protection against moisture and chemicals
- Coated vessels are suitable for non-aggressive water systems or applications with controlled environments
- This is a cost-effective pressure vessel corrosion protection option when stainless steel or FRP isn’t feasible
However, coating integrity must be monitored over time. Damage or wear in coatings can expose the underlying steel, compromising pressure vessel corrosion protection.
For best practices on maintaining coated and uncoated pressure vessels, consult Environmental Expert’s guide on maintenance.
Benefits of Using Corrosion-Resistant Materials
Choosing corrosion-resistant materials for your water pressure vessels brings long-term advantages that go far beyond basic pressure vessel corrosion protection.
Longevity: Extends Vessel Life and Lowers Lifecycle Costs
Materials like stainless steel and FRP don’t just delay corrosion—they actively provide pressure vessel corrosion protection. This significantly increases the lifespan of your equipment, delaying the need for replacements and reducing total ownership costs. Understanding the rich history of pressure vessel design helps appreciate how pressure vessel corrosion protection strategies have evolved.
Safety: Prevents Catastrophic Failures and Protects Personnel
Effective pressure vessel corrosion protection helps maintain vessel integrity under stress, protecting workers and systems from unexpected failures or ruptures. This safety factor is critical in industries handling high-pressure fluids or chemicals.
Efficiency: Reduces Downtime, Increases Reliability
Downtime due to leaks, repairs, or inspections is expensive. Vessels with proper pressure vessel corrosion protection are more reliable, keeping your systems running without interruption. For faster project delivery, consider prefabrication solutions that can reduce installation time and minimize operational disruptions.
Compliance: Meets Regulatory Standards for Health, Safety, and Environment
Many industries require compliance with ASME, API, or OSHA standards, especially when dealing with potable water or hazardous materials. Proper pressure vessel corrosion protection supports compliance and peace of mind during audits or inspections. Learn more about our comprehensive capabilities in meeting industry standards.
The Importance of Corrosion-Resistant Materials in Water Pressure Vessels
Selecting appropriate corrosion-resistant materials for water pressure vessels is a critical investment that extends far beyond initial costs. Whether choosing stainless steel, duplex stainless steel, FRP, or coated carbon steel, the right material selection directly impacts vessel longevity, operational safety, and regulatory compliance. Proactive corrosion protection strategies deliver measurable returns through extended equipment life, reduced maintenance costs, and enhanced reliability. Organizations must balance immediate budget constraints with long-term operational demands and safety requirements. Ultimately, investing in proper pressure vessel corrosion protection ensures reliable performance while minimizing lifecycle costs and operational risks across all industrial applications.
Need a reliable partner?
Red River specializes in the design and manufacturing of pressure vessels. We also fabricate related items such as prefabricated spools and skid packages.
Reach out to us today and experience the Red River difference. Where American-made products and American Values come together, we care more.
Frequently Asked Questions (FAQ)
1. What is the most effective pressure vessel corrosion protection method?
Duplex stainless steel provides superior pressure vessel corrosion protection.
2. How do I implement pressure vessel corrosion protection in existing systems?
Our pressure vessel fabrication team recommends optimal pressure vessel corrosion protection strategies.
3. What are the costs associated with pressure vessel corrosion protection?
Proper pressure vessel corrosion protection reduces long-term maintenance costs significantly.
4. How often should pressure vessel corrosion protection be inspected?
Regular monitoring ensures effective pressure vessel corrosion protection throughout lifecycle.
5. Can pressure vessel corrosion protection be retrofitted to older vessels?
Pressure vessel corrosion protection retrofitting through coatings requests a quote.
6. What industries benefit most from advanced pressure vessel corrosion protection?
Aggressive environments benefit significantly from advanced pressure vessel corrosion protection and learn secrets.
Key Takeaways
- Corrosion can compromise vessel safety and performance, but it’s preventable with the right pressure vessel corrosion protection strategy
- Stainless steel, duplex stainless, FRP, and coated carbon steel each offer unique pressure vessel corrosion protection benefits depending on your application
- Long-term costs are reduced when pressure vessel corrosion protection is addressed proactively, not reactively
- The best pressure vessel corrosion protection method depends on pressure, temperature, chemical exposure, and budget—there is no one-size-fits-all solution
- Investing in pressure vessel corrosion protection is investing in safety, reliability, and operational success
- For specialized applications requiring advanced pressure vessel corrosion protection, consider our modular skids solutions that integrate multiple components into pre-tested, factory-assembled units.